AI and IoT empowered Predictive Maintenance
Today’s maintenance, reliability and digitization teams are leveraging AI and IoT driven Predictive Maintenance to bring digital transformation to their maintenance practice.
What is predictive maintenance?
Predictive maintenance (PdM) is maintenance that measures the performance and condition of equipment of in-service equipment during normal operation to identify any faults developing. It provides cost savings and better reliability over routine or time-based preventive maintenance.
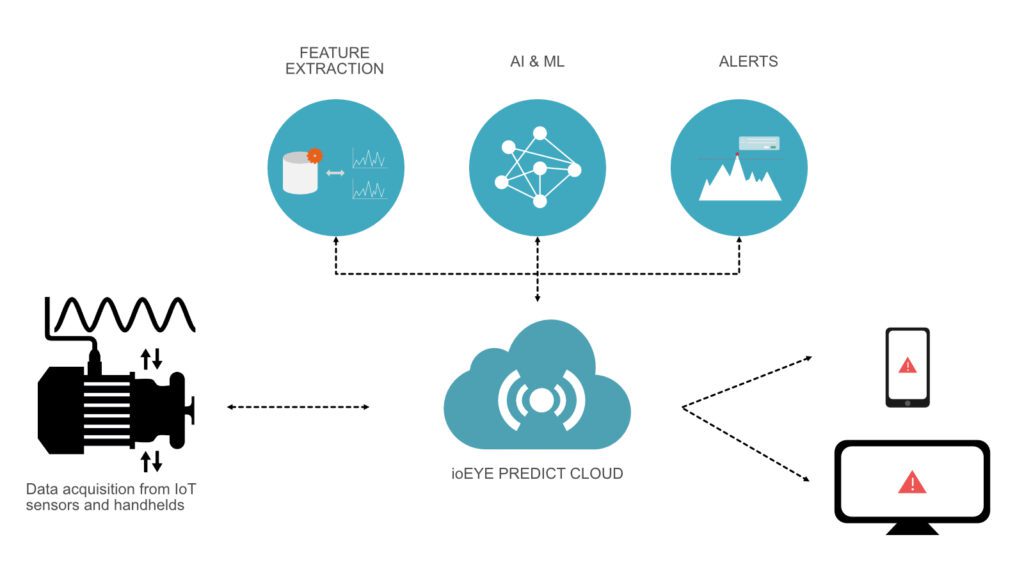
Where should i use it?
Planned Maintenance
(PM)
For assets whose failures modes increases with time or use and can be prevented with regular maintenance e.g. valves
Predictive Maintenance
(PdM)
For assets whose failures modes increases with the condition of operation and can be prevented with monitoring/measurements e.g. rotating and reciprocating
Reliability Centered Maintenance
(RCM)
For assets whose failures modes are identifiable and controllable e.g. aircraft engines , large turbines.
Where does it fit in your maintenance strategy?
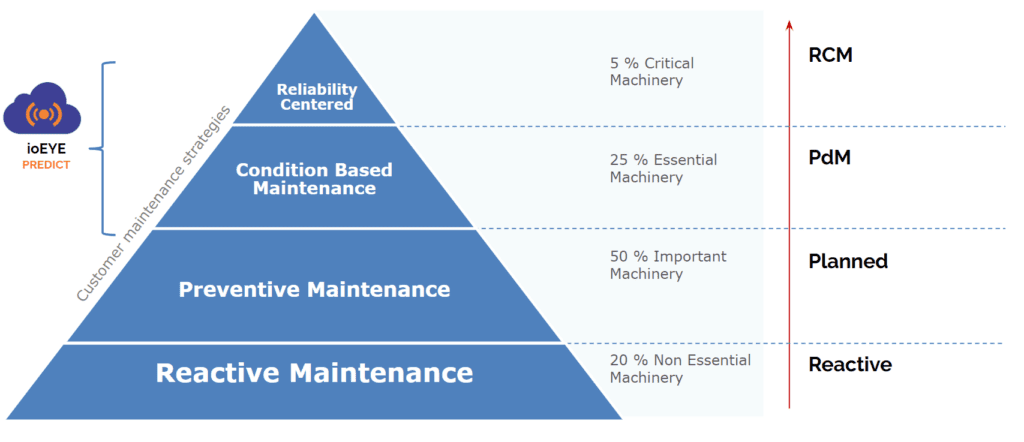
Common PdM Tools
Root Cause Analysis (RCA) makes PdM even more powerful
The goal of predictive maintenance is to measure equipment condition and then predict its failure, followed by a root cause analysis and then preventing the failure through corrective maintenance.
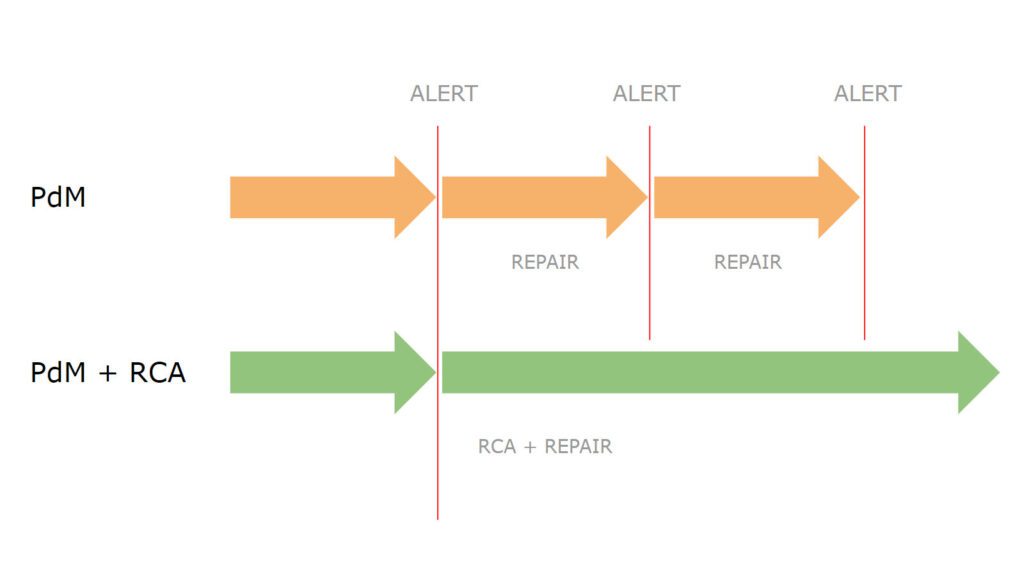
Want to get started with ioEYE Predict?
Now is the right time to change how we sense, predict and troubleshoot machine failures
IIoT sensor technology has made it possible to measure machine condition parameters like vibration, ultrasound, temperature, etc affordably and without human intervention. Machine-learning models can increase the accuracy of the predictions and make it easy for the maintenance team to run the program across a large number of equipment with minimal knowledge of condition monitoring techniques.
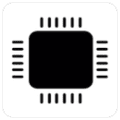
CHEAPER HARDWARE
Affordable sensor and microcontroller technologies.
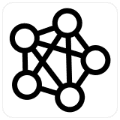
RELIABLE CONNECTIVITY
IoT is making sensor connectivity easier, secure and more reliable.
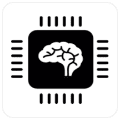
SMARTER ALGORITHMS
Machine Learning(ML), Artificial Intelligence(AI) and Bi Data are making predictions possible.
Benefits of IoT and ML driven digital transformation in maintenance
machine learning predicitve maintenance
Choose a new and better way to maintenance
ioEYE Predict makes PdM affordable and even more powerful
IoT Sensor
ACQUIRE CONTINEOUS MACHINE HEALTH DATA
ML & AI
PREDICT FAULTS ACCURATELY
AUTONOMOUS
Now collect asset predictive maintenance data without human intervention and error, 24 x 7. Free up the time your team spends on data collection via an handheld.
ANYWHERE
Now access your machine’s health and diagnostic data from anywhere using a mobile phone. Digital transformation for your maintenance team.
ADVANCE
ioEYE Predicts assist you in identifying machines that need attention. The area where they need attention. The advance analytical tools can help you do a root cause analysis and support your decisions.
AFFORDABLE
We have used the latest technology while striking a balance between affordability and features. It is designed to get the work done cost effectively.