Predictive Maintenance Defined- Procedure
What are its advantages?
Maintenance is a tough and hectic job inside manufacturing industries for the maintenance personals working there. This is because the constant fear of unexpected breakdown or failure of critical machines is always present. Fortunately, the IoT Based Maintenance called Predictive Maintenance provides a solution.
In this post, you will know about Predictive Maintenance technology, its advantages, disadvantages, how it’s implemented, and how it’s going to shape the way of industrial maintenance.
To start with, if we talk about unexpected breakdowns inside manufacturing industries, it leads to high downtime of the critical machines. It adversely affects the production process and causes huge financial losses for industrial firms.
In fact, data from several studies have shown that the unexpected machinery breakdown results in a loss of more than USD 50 billion to manufacturing industries. This is a huge monetary loss that these companies can avoid if they use PdM technology, which is the modern and innovative way of planning maintenance tasks inside the plants.
But if we go deeper into the understanding of PdM, then it’s not really something very new or unknown. The condition-based maintenance which is the core of PdM Technology was there from the early ’90s.
And going way past in time, a mechanic touching his machine with his hands or keeping his ear near the screwdriver, and then “predicting” the fault of bearing or another part when hearing or sensing unusual vibration or sound, is nothing but the art of Predictive Maintenance in practice.
In Predictive Maintenance, the assets/machines are wirelessly monitored to detect the developing faults or early failures in them. The maintenance or repair of those assets is then planned accordingly.
What is Predictive Maintenance(PdM)?
Predictive Maintenance can be defined as a type of maintenance method that uses condition monitoring tools to create a maintenance or repair plan prior to the full machine failure or breakdown.
Here, you will be able to plan your maintenance with the help of alerts that will be generated by the predictive maintenance system deployed on your machinery. This will ensure that you are performing the repair activities only when it is required.
So in short, we can also say that here, you will be able to perform what we can call Alert Based Maintenance.
How Predictive Maintenance is done?
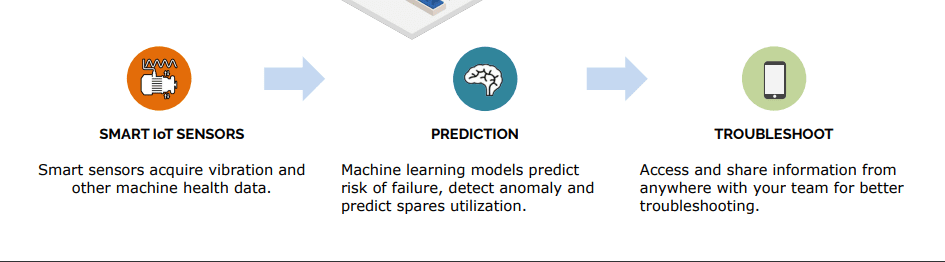
Predictive Maintenance uses the Internet of Things (IoT) for its existence and functionality.
IoT is defined as an ecosystem of interrelated physical devices provided with unique identifiers (UID), which makes them capable of communicating within themselves without any human-to-human or human-to-device interaction.
Predictive Maintenance technology uses a combination of sensors and software.
A sensor or combination of two or more sensors is required to accurately monitor essential parameters like Vibration, Temperature, Magnetic Flux, Ultrasound, etc. These parameters describe the health condition of machinery.
These sensors are integrated with the software modules completing the whole IoT ecosystem, and the data captured is stored and analyzed to detect machine failures.
As described earlier, the PdM Platform generates alerts whenever any parameters exceed their acceptable limits. The acceptable boundaries of parameters for a healthy machine operation are defined within the system. This allows the system to generate an alert or trigger an email notification whenever those values exceed their threshold limits.
So, by adequate monitoring and various analysis techniques like Vibration Analysis, Ultrasonic Analysis, Temperature Analysis, Oil Analysis, Boroscope Analysis, Infrared(IR) Analysis, and Magnetic Flux Analysis, various faults occurring in the rotating machines like Unbalance, Misalignment, Bent Shafts, Bearing Faults, etc can be detected.
Read on Vibration Analysis and Ultrasound Analysis.
If we talk about how the threshold values or acceptable boundaries are defined for machinery, then there are basically a few ways for that.
1. ISO 10816 Vibration Severity Chart – For Vibration Analysis
The threshold values for failure vibration can be determined on the basis of the standard vibration severity chart called ISO 10816.
2. Manual Data Entry
You can also define the threshold values manually with the help of the datasheet created on the basis of the conventional condition monitoring technique.
To create your own datasheet of machine failure values, you need to establish a relation between the measurable parameters, eg. vibration, temperature, flux, etc, and the component life. For that, take readings at equal intervals until the machine fails. Repeat the process several times and then take the average failure value to feed into the PdM system.
3. ML/AI Algorithms
The most accurate and interesting part is the ML/AI algorithms for detecting faults and generating respective alerts.
In fact, this is the only reason that differentiates this sensor and software platform from the conventional manual condition monitoring method, and also gives this complete IoT platform the name Predictive Maintenance Platform.
The sensors deployed on the machinery will closely observe that asset and then define the threshold values by proper analysis of the parameters for the most accurate fault prediction.
Where Predictive Maintenance can be deployed?
All types of critical rotating or reciprocating machines that have
1. High repair time due to Preventive or Reactive Maintenance
2. High maintenance or repair costs involved
3. Direct impact on the production cycle
are good candidates for Predictive Maintenance Solution.
So you can use this for your high capacity Motors, Pumps, Compressors, Fans, Gearboxes, etc.
Moreover, PdM has got its application in various industries like railways, manufacturing, and the oil and gas sector.
What are the conventional maintenance methods used in industries?
The conventional Maintenance methodology that is currently followed across the manufacturing industries is Preventive Maintenance, which comprises run-hour maintenance and Periodic (Scheduled) Maintenance.
Reactive Maintenance or repairing an asset after its total failure is also performed but on smaller or non-critical machinery.
How Predictive Maintenance differs from Conventional Maintenance strategies?
In Predictive or condition-based maintenance, you perform your repair activities only when your machine shows major signs of its deterioration. The machine deterioration can result either due to its constant operation or its mishandling by the operator.
As described above, the PdM system provides you with essential alerts with the help of which the maintenance or repair work is then planned or performed.
What are the benefits of using Predictive Maintenance Technology?
There are many benefits or advantages of the predictive maintenance technique over the conventional maintenance methods, and companies that know have started using this technology.
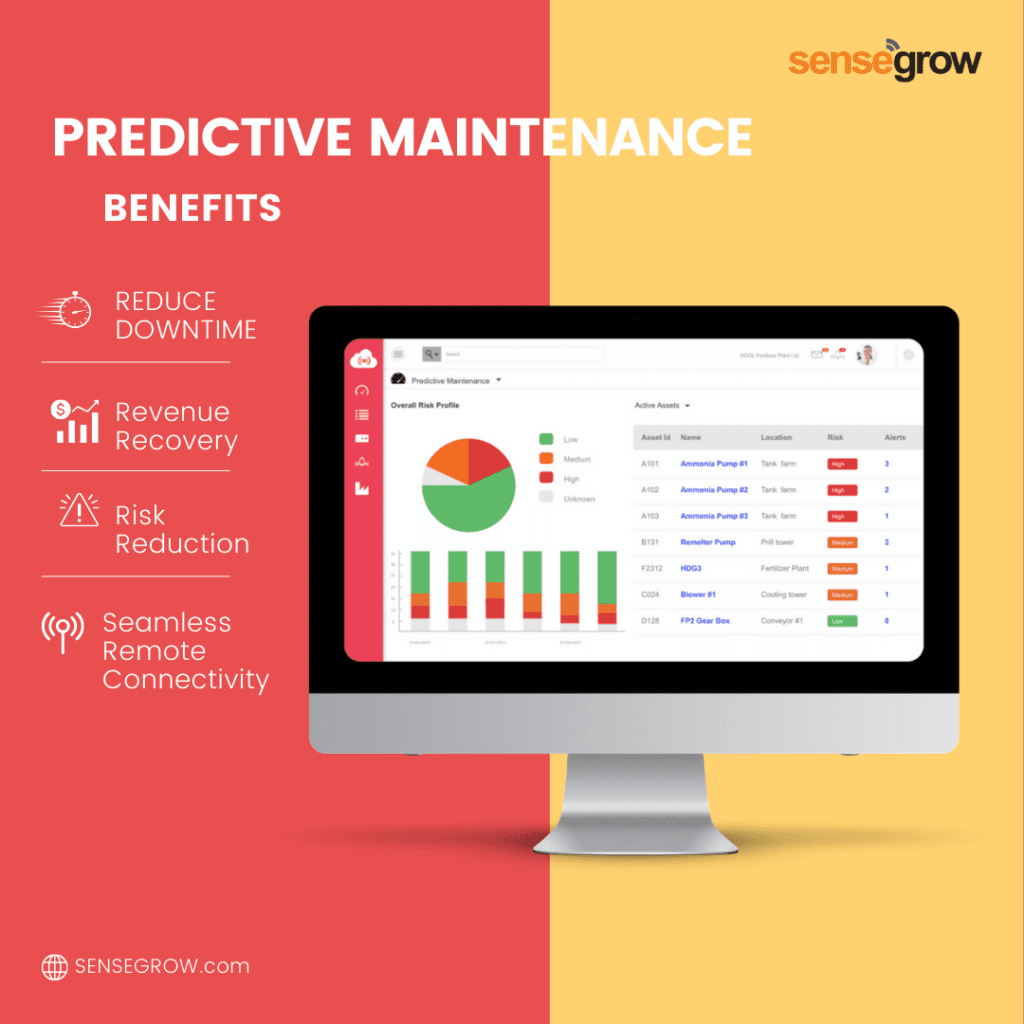
One such example is Rio Tinto, which is the world’s 2nd largest mining firm and using the Predictive Maintenance based approach, they are able to make a profit of 2 million USD daily.
Here, take a read on 5 major advantages of predictive maintenance that give the reason for manufacturing industries to adopt this technology inside their plant premises.
1. Predictive Maintenance Offers 24X7 Remote Machine Monitoring
Predictive maintenance benefits by allowing you to monitor your machines 24X7 from anywhere and at any time.
So now you don’t need to visit your machines each time for a routine check-up. This provides you with comfort over that hectic maintenance schedule. And reduces that unplanned repair tasks, up to 75% as per several data available.
Also, your maintenance will now be planned each time and will be done only when required due to the presence of machine-insights with you.
2. Reduces The Overall Maintenance Costs
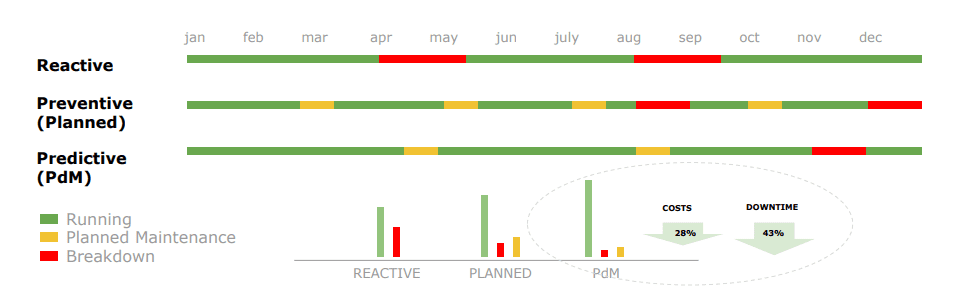
One of the main advantages of predictive maintenance is that it reduces the maintenance costs spent on critical machines.
An initial investment of installing the setup is required, but in the longer run, it can give you up to 10 times of Return On Investment(ROI). Data from several studies have shown a minimum decrease of 25% in overall maintenance costs across industries.
Further, it is also found that preventive maintenance costs around $16 per horsepower per year, reactive maintenance costs $21 per horsepower per year while predictive maintenance costs $10 per year.
You can’t plan on breakdown repairs. So you need more time and effort to fix them. They can also cause a “ripple effect” where the other finely operating machines down the line are also damaged due to the damage of single machinery.
Planned maintenance in Preventive Maintenance is not only hectic but also adds maintenance costs over time.
3. Also Improves Production Cycle
Using predictive maintenance in manufacturing plants helps in increasing the productivity of machines. It allows the machines to operate continuously now without any interruption.
So you can avoid the production losses due to the routine repairs as your machines are now under continuous observation. The maintenance will be done only when it is required. In fact, it is observed the downtime impact to reduce by (40-45)% as compared to the preventive maintenance schedule.
4. Increases The Life Of A Machinery
The constant reopening of machines affects their life. But Predictive Maintenance benefits hereby reducing the frequent re-opening of machine parts. This, in turn, improves their lifespan.
Also, the whole machine and its components can now be repaired, oiled, or greased in a better way. As you will be able to know the accurate condition of the machine components.
5. Helps In Maintaining The Spare Parts Inventory
One more way the PdM benefits in your repair work is it helps to maintain the inventory of your machine components.
This is because now you are knowing the faults more specifically and the location where it is developing inside your machinery. You can purchase a new machine part when you need it. As you know are scheduling your maintenance when it is required.
So, above were the 5 major advantages of using Predictive Maintenance at the manufacturing plants.
There is no doubt that our world is rapidly becoming digital. The way we were doing shopping 10 years back is not the same as we do now. The demand for IoT products is increasing at its full pace as we desire convenience in whatever tasks we do. Many things have become digitized and sooner or later, the maintenance practices will also transform completely from their current ways.
If you are looking for a PdM Platform for your machines, then we at SenseGrow offer :
ioEYE Predict: The Vibration Monitoring IoT Platform.
Our ioEYE Sensor also monitors parameters like Ultrasound, Temperature, Magnetic Flux apart from the Machine Vibrations.
The platform will show you the health condition of your rotating machines on our SaaS cloud platform ioEYE Predict, which will help you to plan your maintenance tasks.
One Comment
Comments are closed.