Centrifugal pumps are widely used in the Industry. Pumps are one of the major contributors to energy consumption and plant breakdown occurrences. Pump operators usually face the following two challenges with centrifugal pumps:
- Poor Efficiency
- Poor Reliability
The solution to the above two problems is simple – Operate the pumps at or near their best efficiency point. Even though this is a widely understood concept most industries will have average pump efficiency of less than 40%. This is way below the 70% to 85% efficiency good performance benchmark. Why is this?
The challenge is effective monitoring and corrective action. Most pumps would have no monitoring system in place leaving the operator in the dark. Secondly where the pumps have a monitoring system it is difficult to continuously plot and analyze pump data. So even when data like pressure, flow, RPM and energy used is available; analyzing it and coming to a conclusion requires a lot of effort and man hours.
So most pumps are left to operate in zones that lead to poor efficiency and reliability. Also a lot of pumps are not right sized, leading to poor efficiency and reliability. This blog explores how to solve this problem with IoT and AI. IoT can be used to collect data and AI can be used to autonomously detect pumps with following issues:
- Operating in poor efficiency zone
- Operating in poor reliability zone
- Frequent start and stops
- Over or Undersized pumps
- Pumps with high operating hours
- Pumps developing faults like cavitation, bearing issues or with other mechanical issues
- Motor and VFD issues and faults
This AiOT solution can then be used to provide the pump operator the right analysis, detection and prescription.
What leads to centrifugal pump inefficiencies and losses?
Centrifugal pump losses can be categorized into three categories:
- Hydraulic – These occur due to the conversion of energy from kinetic to potential or vice versa within the pump. Hydraulic losses occur at the inlet, outlet, and in the impeller.
- Volumetric – Leakage through internal and external clearances of components of the pump.
- Mechanical – These occur due to the inefficiencies in the mechanical components of the pump, such as bearings, seals, and couplings. Mechanical losses can result from friction, wear, vibration, looseness, misalignment, disk friction, bearing, coupling etc.
Total loss = Hydraulic + Volumetric + Mechanical |
These losses are not constant and are dependent on the pump speed and head. We can see in the below diagram that for a constant head the losses increase as pump speed increases and decreases below an optimum speed range.
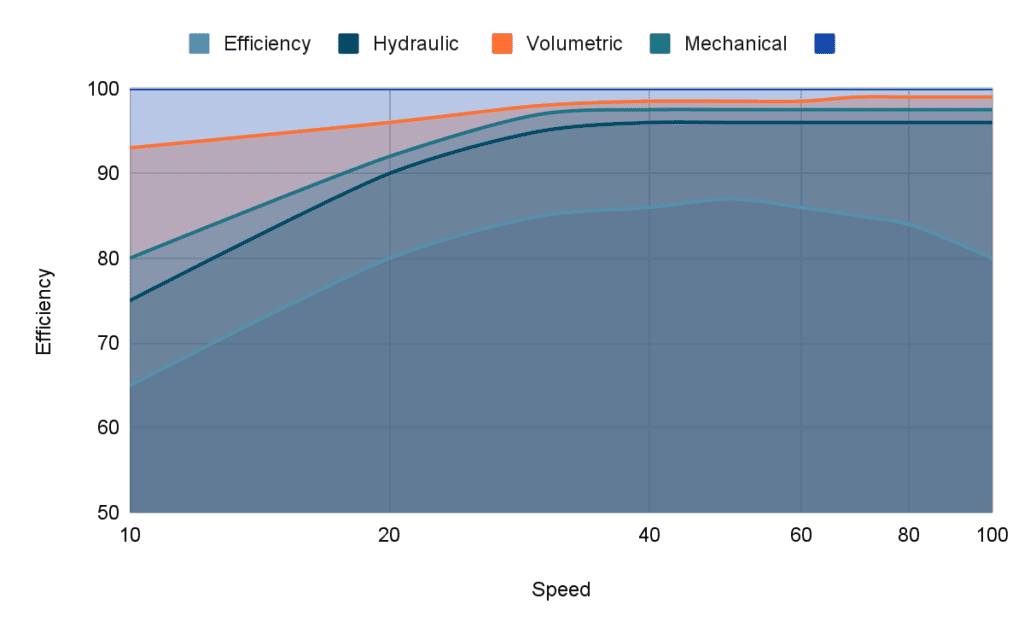
So what is the recommended operation range for best efficiency?
As discussed in the above section pump losses are dependent on the pump speed. So how do we know what is the best operating speed of the pump for efficient operations?
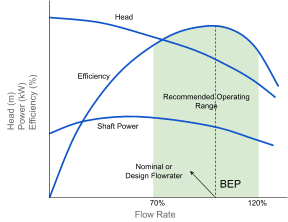
The recommended operating range for a pump is between 70% to 120% of its BEP flow rate. But at flow rates below 70% there is excessive vibration in the pump and at flow rates above 120% expect cavitation. This recommended operating range is defined in standards such as Hydraulic Institute Standards (HI) or American Petroleum Institute Standard 610 (API 610). These are typical values and do vary on the type of impeller and the piping system. In some high energy pumps this range is in between 80% to 115% of BEP flow rate.
But this flow control is best achieved by the pump speed instead of throttling the discharge valve. Throttling the discharge valve will usually lead to waste of energy and reduction in efficiency and reliability. This is best achieved with a Variable Frequency Drive (VFD). Operating a pump close to its BEP is good for both efficiency and reliability of the centrifugal pump. Reducing the speed of the pump moves the BEP to the left allowing you to operate the pump efficiently and reliably at a lower flow rate.
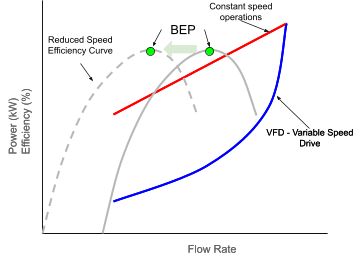
How do you achieve and ensure a high pump efficiency and pump reliability?
Pump reliability and efficiency depend on its operating flow rate and head. When the pumps are operated at their BEP they have higher reliability and efficiency for a given head. The illustration below plots the relationship between a centrifugal pump flow rate and pump reliability. Operating the centrifugal pump at the Best Efficiency Point (BEP) leads to higher reliability. The best industry practice is to operate pumps at between 90% to 105% of BEP to ensure good reliability. From hundreds of installations monitored by ioEYE Predict we have observed that most industrial pumps operate outside these BEP specifications. The further away a pump operates from its BEP the lower is its reliability. This is one of the leading causes of high energy consumption and poor reliability of centrifugal pumps.
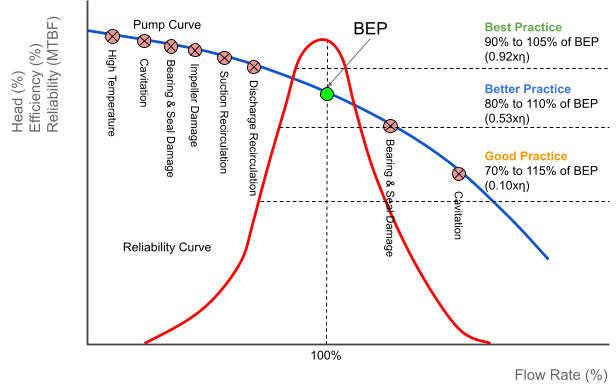
Operating pumps outside their reliability curve can cause various issues. While operating them outside the pump performance curve can cause efficiency to fall. These curves depend on the pump design, power, suction and discharge head, and speed. The key issues caused by operating pumps outside the reliability curve are:
1. Temperature Related Damage: When a pump is operated at a very low flow rate, most of the input power input gets converted to thermal energy. This causes rapid temperature rise. Temperature rise for extended periods can cause failure of the rotating parts or irreversible damage to the pump. A pump should not be operated below 15% of the BEP flow to prevent temperature rise.
2. Bearing and Seal Damage: If the pump is operated at low or high flow rate bearing and seal damage can occur. Low and higher than recommended flow rate can lead to unbalance, vibrations, and high shaft force which in turn increase stresses on the bearings. Consult the OEM recommendation of flow rate for preventing bearing and seal damage.
3. Suction and Discharge Recirculation Damage: When the flow of a pump is reduced, e.g. by throttling or due to increased head, recirculation can occur. All pumps, based on their impeller design, have a flow limit at which recirculation occurs. Recirculation is flow reversal at the suction or the discharge tips of the impeller vanes. It occurs at a reduced flow rate below the pump BEP. Recirculation may cause increased noise, vibration, stresses on the impeller, shaft seal and bearing.
4. Cavitation and Impeller Damage: Recirculation causes damage due to cavitation, pressure pulsations and vibration. Cavitation leads to formation of bubbles. These bubbles reduce the output of the pump while increasing vibration and noise. When these bubbles implode they release bursts of energy that cause severe erosion in pump components, like in the impeller.
Most pump operators know the BEP from the pump performance curves, but knowing the BEP is not enough. The operator needs to monitor the BEP in real time and know if the pump is operating near its BEP. This requires sensors or meters to be installed to monitor pump flow rate, head and its power. Secondly it’s not humanly possible to analyze this data continuously across all the pumps in your facility. IoT and AI or what you collectively now call AIoT can help.
How solutions powered by IoT and AI (AioT) can be used to improve pump efficiency and reliability?
IoT can help you capture data from centrifugal pumps regularly for BEP calculations. It can be better than a SCADA and DCS system as you can capture more detailed data like current and voltage spectrums for detecting and predicting faults. You can also leverage this data using cloud powered AI models for predictive analytics and identifying pumps that are not operating at their BEP or developing faults. AI allows prediction capabilities and also prescriptive capabilities.
Why does an IoT and AI driven centrifugal pump optimization system make business sense?
Pumping systems contribute to significant energy (55%) and maintenance costs (30%) in an Industrial facility. The operating and maintenance costs are the largest contributor to the cost of the pumping system. In most industries pumping systems are not right sized and this oversized system leads to pumps being operated further away from their BEP. As explained earlier this leads to excess energy use and reduced life of the pumping system due to excess vibration, temperature and cavitation. Increasing energy and maintenance costs, while reducing the pumping system life.
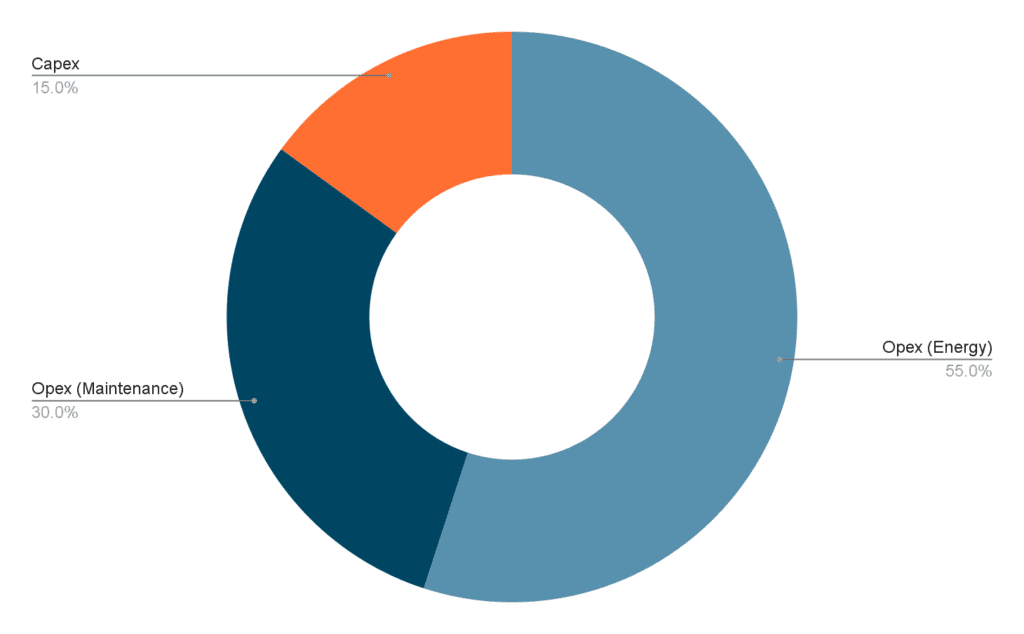
As we can see in the above there is scope of reducing costs by 20% to 40% through pump optimization. An IoT and AI system can help you realize these savings. The system can also detect incipient faults 4-5 months in advance. This can lead to further saving in production loss due to unplanned downtime. The system works as follows:
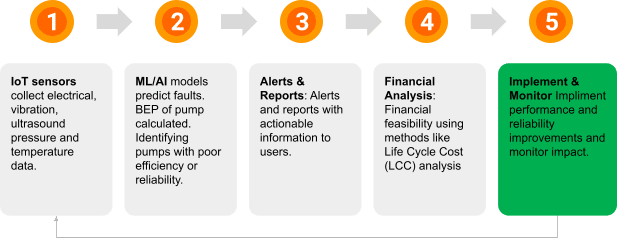
This optimization cycle has to be an ongoing continuous process. Using IoT and AI to make it autonomous, ongoing and prescriptive. An IoT and AI based centrifugal pump optimization system can improve outcomes without increasing the workload of the team. Usual payback for the system can be achieved within 5 to 6 months.
How can ioEYE Predict help you improve centrifugal pump efficiency and reliability affordably?
ioEYE Predict allows you to use multiple AI models for predicting pump faults and algorithms to calculate its real time BEP. It can calculate BEP in multiple ways using a combination of power, flow, head or speed data. If you already are monitoring these parameters you can send this data to us. If you are not monitoring these parameters you can use our ESA (Electrical Signature Analysis) sensor to monitor these parameters and calculate real time BEP.
With the ESA solution you can also detect and predict faults using the current and voltage spectrum. This allows a comprehensive solution for predicting the faults developing in the pump and motor while also ensuring the pump is operating at its BEP. The system AI models monitor and predict these faults, estimate reliability and detect efficiency issues. It then sends out an alert or weekly report to you for proactive corrective action. These corrective actions once implemented lead to a reduced energy consumption and improved reliability of your centrifugal pumps. Energy savings of 20% to 40% are typically achievable after implementing the recommendations made.