Total Productive Maintenance (TPM) is a way to keep equipment running smoothly without any problems. The goal is to have no breakdowns, no slowdowns, no defects, and no accidents. TPM tries to make equipment work as well as possible by taking care of it before problems happen.
Principles of TPM
TPM aims to create a culture of continuous improvement and reliability across the organization, leading to increased productivity, reduced costs, and improved product quality.
- Focused Improvement
- Objective: Eliminate losses and improve processes.
- Activities: Identify and eliminate root causes of equipment inefficiencies. Focus on small, incremental improvements with cross-functional teams
2. Autonomous Maintenance
- Objective: Empower operators to handle routine maintenance of their equipment.
- Activities: Train operators for basic tasks like cleaning, lubrication, inspection, and minor repairs. Establish standardized procedures and schedules.
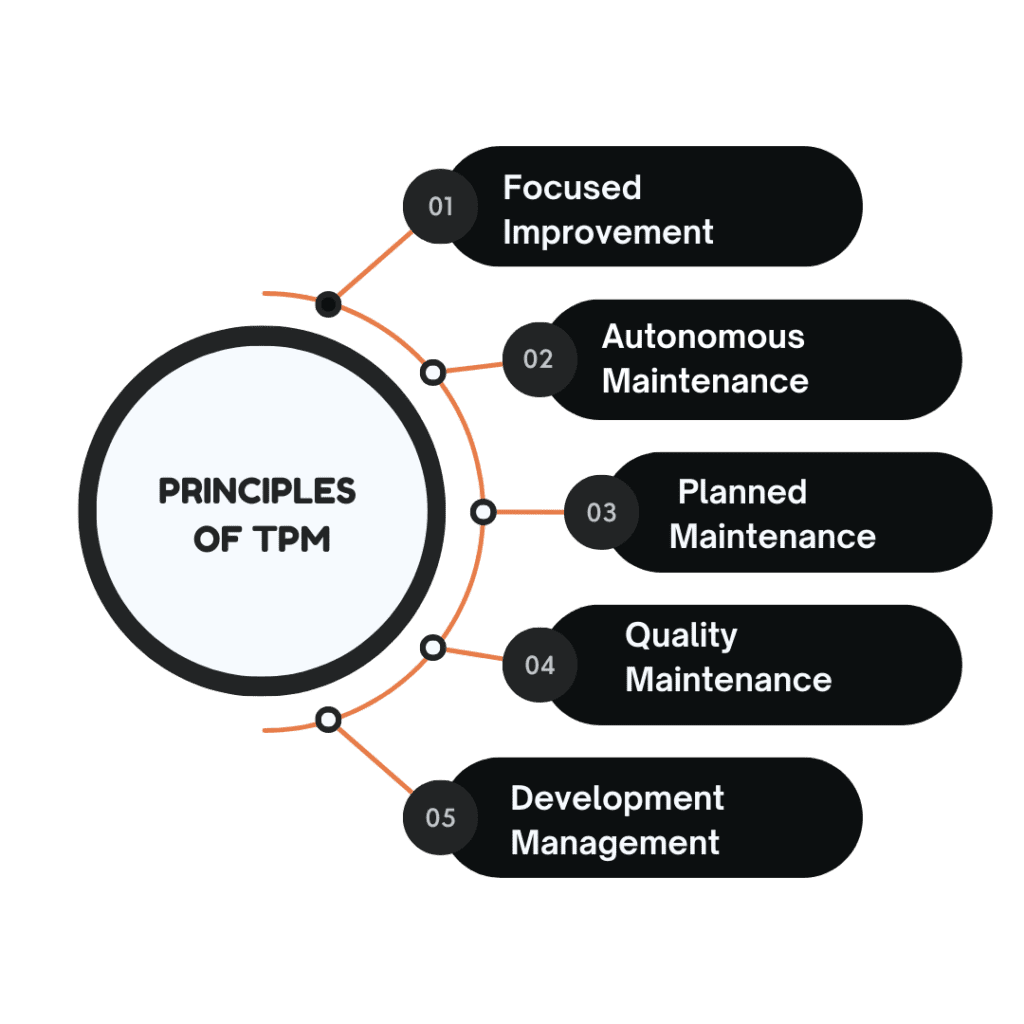
3. Planned Maintenance
- Objective: Prevent equipment failures and extend equipment life.
- Activities: Develop a proactive maintenance schedule using equipment history and performance data. Employ preventive maintenance techniques like condition monitoring and predictive maintenance.
4. Quality Maintenance
- Objective: Ensure equipment consistently produces high-quality products.
- Activities: Identify and eliminate root causes of quality defects. Use statistical process control (SPC) and other quality management tools to monitor and control equipment performance.
5. Development Management
- Objective: Ensure the effective implementation and sustainability of TPM.
- Activities: Establish a clear vision and goals for TPM. Create a structured implementation plan, monitor progress, and celebrate successes.
What are the Key benefits of implementing TPM?
Implementing Total Productive Maintenance (TPM) offers several important benefits:
1. Increased Equipment Reliability and Uptime : TPM helps ensure that machines and equipment run smoothly and without interruptions, leading to more consistent and reliable production.
2. Improved Product Quality : By maintaining equipment properly and regularly checking for issues, TPM helps in producing products with fewer defects, resulting in higher quality.
3. Reduced Breakdowns and Maintenance Costs : Regular maintenance and early detection of potential problems mean fewer unexpected breakdowns. This not only keeps production on track but also reduces the cost of emergency repairs and downtime.
What is the Implementation process of Total Productive Maintenance?
Following these steps helps improve equipment reliability, boost productivity, and enhance overall operational efficiency.
1. Management Support : .Ensure top leaders are committed and ready to support TPM with resources.
2. Form a Team: Assemble a cross-functional team with representatives from various departments to lead TPM efforts.
3. Training: Conduct comprehensive training for all employees on TPM principles, benefits, and practices.
4. Assess Equipment: Evaluate current equipment performance, identify issues, and gather data on downtime, maintenance, and other relevant metrics.
5. Develop and Implement a Plan: Create and execute a detailed TPM plan outlining steps, timelines, and goals for implementing TPM pillars like autonomous maintenance, planned maintenance, and quality maintenance. Empower operators to perform basic maintenance tasks and establish a structured maintenance schedule.
6. Track Progress: Monitor key performance indicators (KPIs) such as Overall Equipment Effectiveness (OEE) and conduct regular audits to ensure TPM activities are on track.
7. Continuous Improvement: Regularly review progress, gather feedback, adjust the TPM plan as needed, and develop standard operating procedures to sustain TPM efforts. Foster a culture of continuous improvement.
Why is TPM Important?
Total Productive Maintenance (TPM) is essential for boosting equipment reliability, reducing downtime, and enhancing productivity. It involves all employees in maintenance, fostering a culture of continuous improvement and cutting maintenance costs.
Integration of Industry 4.0 Technologies
Industry 4.0 technologies like IoT, big data analytics, and machine learning enhance TPM by providing real-time equipment performance data. This allows for precise, efficient maintenance planning, aligning with TPM’s goals of maximizing efficiency and minimizing downtime.
Predictive and Proactive Maintenance Advancements
Predictive maintenance uses data analytics to foresee equipment failures, enabling proactive measures to prevent breakdowns. Combined with TPM, it ensures optimal equipment condition. Proactive maintenance addresses root causes of failures, further improving reliability, reducing costs, and boosting operational efficiency.