Effective ways to reduce plant downtime and increase productivity in the manufacturing plants are enlisted below –
- Condition Based Maintenance
- Predictive Maintenance
- CMMS and EAMs
- Reactive / Protective (SCADA/DCS), Vibration Switch, Tripping System etc.
Downtime is the loss of productivity in manufacturing industries due to the lack of equipment maintenance, real-time machine health data insights and human error. It is one of the most critical issues in the processes and operations of a manufacturing plant. There are many ways you can reduce downtime and one of the easiest way is integrating “ IoT technology” as they have proven to be very helpful while working on improving productivity in manufacturing plants.
What are the types of downtime?
There are two types of it :
- Planned Downtime
- Unplanned Downtime
Planned downtime:- It is scheduled according to your time and you expect downtime at the time for any reason other than machinery error. It helps us organize, schedule, and prepare for the downtime. While the process is down, the maintenance team can coordinate with contractors, and schedule other tasks to execute. Planned downs can be structured so that the machinery can be cleaned and repaired.
Unplanned Downtime :- It occurs when the machinery is not in working condition due to machine part breakage, power failure, human error, software or system issue. Unplanned downtime increases production loss, production cost and increases maintenance costs.
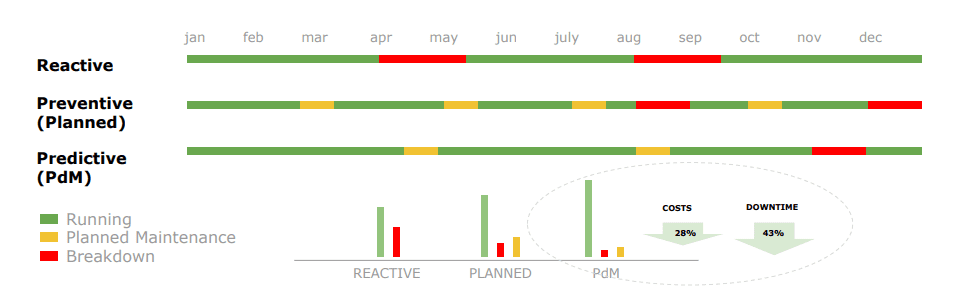
How do you reduce plant downtime?
If you are looking for a way to reduce downtime then you have a variety of options. IoEYE Predict is one the best solutions for effective and instant results. IoEYE Predict is the maintenance that measures the performance and condition of equipment of in-service equipment during normal operation to identify any developing faults. It provides cost savings and better reliability over routine or time-based preventive measures.

How IoT Sensors help you in increasing productivity?
What are the factors influencing Downtime?
The following reasons can cause the downtime in your manufacturing plant.
Component / Equipment Failure :- Equipment failure can be caused by multiple reasons such as Component Aging and Obsolescence, Shutdowns, Temperature Extremes, Vibration and Shock and component malfunctioning. These failures result in interrupting the process, increase maintenance cost and downtime of the plant.
Maintenance or Repair Work Failure :- Inadequate or improper maintenance practices can lead to machinery failures. Skipping regular maintenance tasks, using incorrect lubricants or replacement parts, or not conducting inspections as recommended can result in unexpected downtime.
Human Error : – Human errors such as incorrect operating behaviors, incorrect settings, improper handling of controls, lack of training, improper handling and loading, neglecting safety protocols. These behaviors might cause equipment failure or interrupt processes, resulting in downtime.
How can our Sensors help you reduce downtime ?

How to Increase Productivity?
Increasing machine productivity involves optimizing the performance and efficiency of machinery to achieve higher output levels while maintaining quality. Some of the strategies which have helped most of the manufacturing plants are regular maintenance, data monitoring, and analysis, predictive maintenance, quality control, employee training.
Most asked questions
-
What is downtime in productivity?
It refers to the period during which a machine or system is not operational, resulting in lost productivity and potential revenue. There are two types of downtime, planned downtime and unplanned downtime. The unplanned downtime can result in major production loss.
-
How do you calculate downtime in manufacturing?
The formula for calculating it is mentioned below:-
Downtime = (Total Downtime / Planned Production Time) * 100% -
How do you calculate KPI downtime?
You can calculate Key Performance Indicators with the help of formula written below –
Total Time = Calendar time between two dates over which calculations are performed
Available Time = Operation Time + Total Downtime
Scheduled Time = Operation Time + Unplanned Downtime
Uptime = Operation Time/Available Time
MTBF = Total Operation Time / Total Number of Unplanned Downtime
MTTR = Total Planned Downtime/ Total Number of Planned Downtime
Total Downtime = Planned Downtime + Unplanned Downtime
OEE = Availability x Performance x Quality -
What are downtime metrics?
Various metrics can calculate downtime such as Overall Equipment Effectiveness (OEE), Mean Time Between Failures (MTBF), Mean Time to Repair (MTTR), Downtime Duration Distribution, Scheduled Downtime Compliance, Emergency Downtime Response Time, Reliability Metrics.
-
How can IoT reduce downtime?
IoT can significantly reduce downtime in various industries by providing real-time monitoring, predictive maintenance, and streamlined operations. It gather, transmit, and analyze data empowers organizations to move from reactive to proactive maintenance strategies. By minimizing downtime, businesses can improve efficiency, customer satisfaction, and profitability while extending the lifecycle of their critical assets.
-
What are the types of equipment downtime?
Equipment failures typically refer to issues that arise during the development, deployment, and maintenance of machine learning models and systems. These failures can lead to degraded performance, inaccurate predictions, and even complete system breakdowns. Types of equipment downtime are
Data Quality Issue
Feature Engineering Problems
Model Selection and Training Issues
Deployment and Production Failures
Monitoring and Maintenance Challenges1