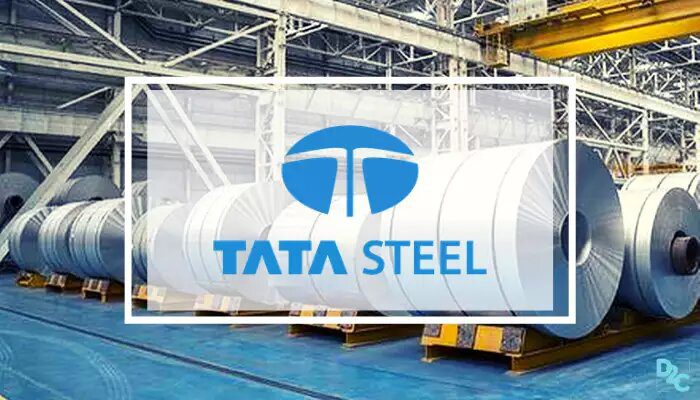
Predictive maintenance in steel plant
Tata Metaliks has merged with Tata Steel.
Tata Steel group is among the top global steel companies with an annual crude steel capacity of 34 million tonnes per annum.It is one of the world’s most geographically-diversified steel producers, with operations and commercial presence across the world. A subsidiary of Tata Steel, Tata Metaliks has a state-of-the-art manufacturing plant in Kharagpur, West Bengal. It produces high quality pig iron and ductile iron pipes in India. It has an annual hot metal production capacity is 500 kt out of 300 kt is pig iron and 200 kt is ductile iron pipes.
predictive maintenance case study
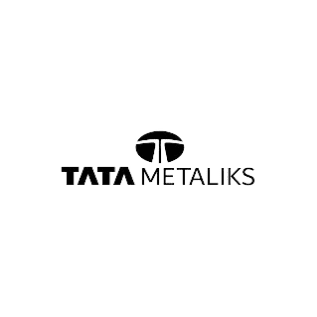
INDUSTRY
Iron and Steel
COMPANY SIZE
$21.34 Bn
YEAR FOUNDED
1994
KEY USE CASES
Early prediction of low RPM gearbox failures in critical sinter machines by leveraging IoT and Artificial Intelligence (AI) for real time condition monitoring and fault prediction.
PRODUCTS & INTEGRATIONS
ioEYE Predict Sensors
ioEYE Predict Predictive maintenance AI Cloud
0%
Downtime due to lack of spares
28%
Reduction in inspection of the gear boxes
Early detection and prediction of gear box failure in sinter machines. These gearbox spares have long lead time. Early detection allows Tata Metaliks to take corrective action and also order gearbox spares in time.
- Minimized downtime while waiting for spares. The system allows them to predict what spares to order.
- Reduced need for inspections in hard-to-access machinery locations.
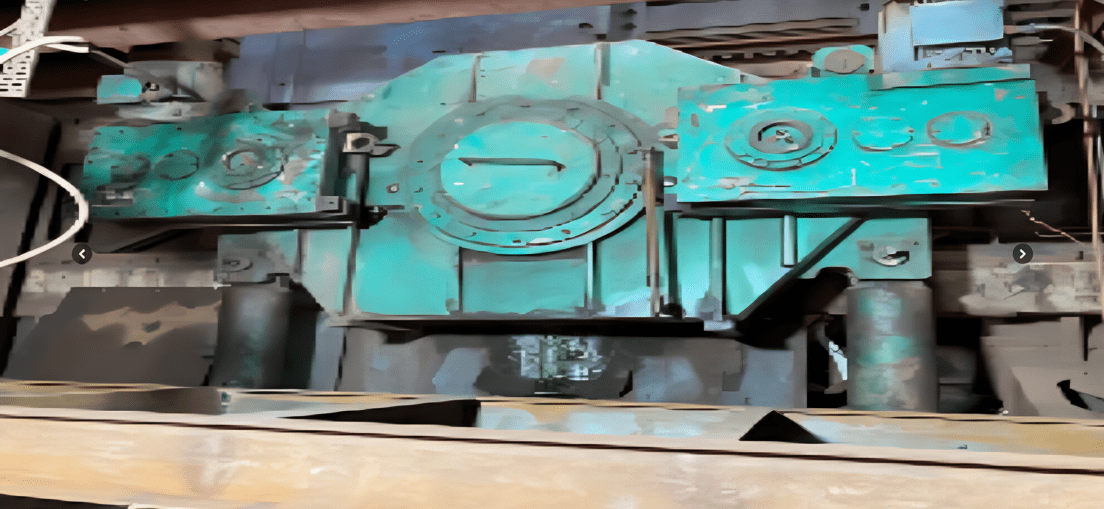
ASSETS COVERED
Sinter Machine Gearboxes
Faults Detected
Challenges
Detecting faults presents a significant challenge in low RPM equipment, primarily because they generate minimal vibrations, thereby complicating the process of fault detection.
The production unit consist of areas that are hard to access every day for detecting faults, which raises the risk of unexpected downtime and the likelihood of machine failures occurring.
Machine Reliability is a major challenge in Iron and steel industry resulting in higher labor costs, increased time consumption, unexpected downtime and lost production.
Outcomes
After implementing the ioeye predictive maintenance solution, the challenge of detecting faults in low RPM equipment, which arises from their minimal vibration output, is effectively addressed.
Production unit machinery was placed in hard-to-access areas, but predictive maintenance solutions enabled Tata Metaliks to monitor their equipment at regular time intervals.
Through predictive analytics, maintenance tasks can be scheduled proactively during planned downtime, minimizing disruptions to production schedules and reducing labour costs associated with reactive maintenance. This proactive approach not only improves machinery reliability but also optimizes operational efficiency by reducing time consumption and mitigating the risk of unexpected downtime and lost production
Digitization and Predictive Maintenance Drove Unprecedented Efficiency and Cost Savings in Steel Industry
Tata Metaliks, a renowned group of the TATA Group, focuses on manufacturing pig iron and ductile iron pipes. The company emphasizes innovation and high standards, contributing significantly to infrastructure development and industrial progress on a local and global scale. Through the utilization of cutting-edge manufacturing techniques and a strong dedication to sustainability, Tata Metaliks continues to be a prominent figure in iron production, actively enriching communities worldwide with progress and prosperity.
For decades, the company has been a pioneer in the production of high-quality pig iron and ductile iron pipes. However, like many industrial leaders, it has encountered challenges, particularly in ensuring the dependability of its aging machinery. To overcome these challenges, the company embarked on a comprehensive digitization program aimed at upgrading its machinery and enhancing overall efficiency.
To overcome these challenges, the company embarked on a comprehensive digitization program aimed at upgrading its machinery and enhancing overall efficiency.
To enhance overall efficiency they needed a proactive approach. Implementing predictive maintenance to achieve these goals, maintenance schedule that included routine inspections, proactive repairs, and early fault detection. In addition to the maintenance program, the team also invested in advanced technologies such as condition monitoring sensors and machine learning algorithms to predict potential failures and optimize maintenance processes. This proactive approach not only increased machine reliability but also improved overall operational efficiency. By prioritizing proactive maintenance strategies and leveraging cutting-edge technologies, the organization was able to maintain peak performance levels and ensure uninterrupted operations.
As weeks turned into months, the true impact of SenseGrow’s solution began to unfold. Tata Metaliks engineers received timely alerts and actionable insights, allowing them to intervene proactively and perform preventive maintenance tasks before equipment failures could occur. Gradually, the frequency of unexpected breakdowns dwindled, and the factory’s overall reliability soared to new heights.
SenseGrow has provided us with a reliable and precise IIOT based solution for predictive maintenance and condition monitoring, the user interface is very friendly and flexible. Unlike other similar solutions, it offers detailed analysis, customized alerts and smart suggestions which have really helped us in the proactive maintenance of our most critical equipment in which faults are not easily detectable. Their active support is undoubtedly the best, where they proactively monitor our assets as well and provide us with training, suggestions, and solutions!
Kirti Kumari
Manager
Explore the products which help our customers grow
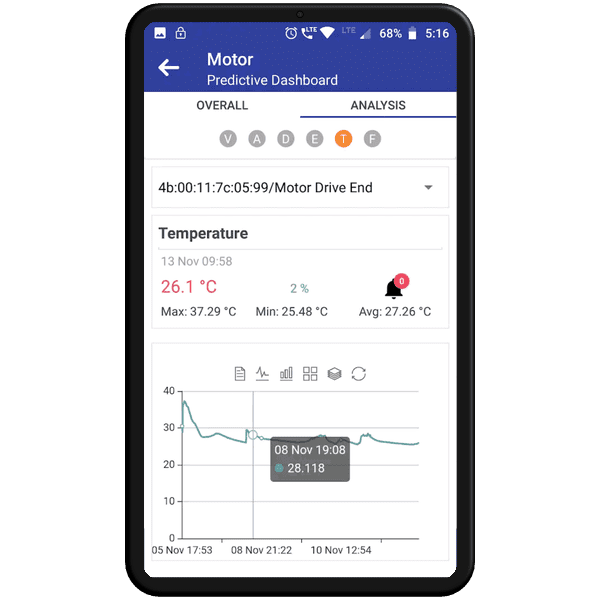
AI and cloud platform for predictive maintenance
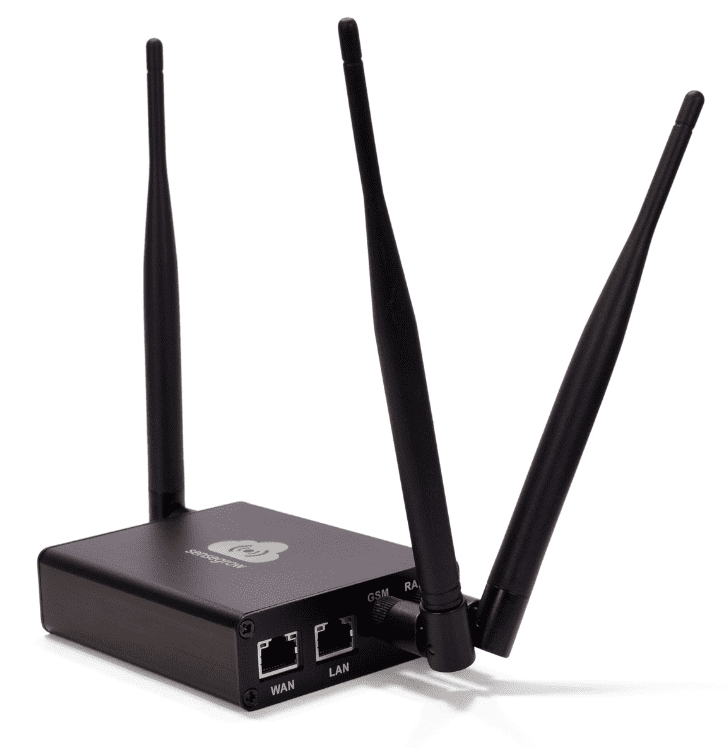
IoEYE Predict Gateway
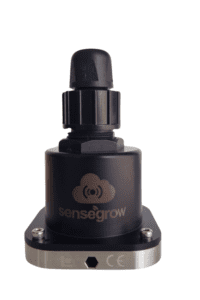